Table Of Content
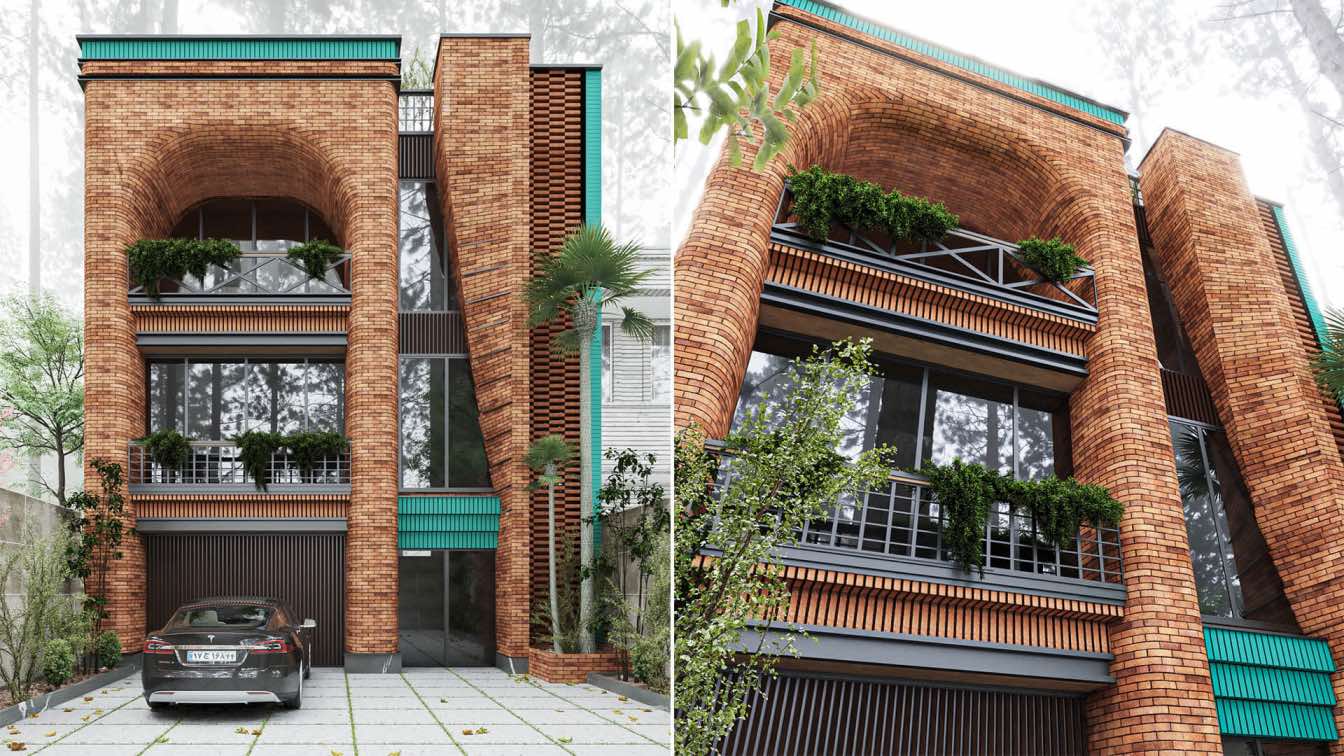
Stucco is also energy efficient, as it has the ability to reflect heat rays, helping to keep homes cool in the summer and warm in the winter. It can reduce energy costs and make homes more energy efficient, which is important for property owners in California, who often face higher energy bills due to the state’s warm climate. Beyond its durability, stucco is also an affordable siding option and is cheaper than many other materials on the market. This is great for property owners looking to make smart investments in their home, as stucco requires little to no maintenance and lasts for many years. Houses in California are typically constructed out of stucco for a variety of reasons. Stucco is a great material for homes in California due to its durability, affordability and energy efficiency.
Where is construction booming California?
Homes are often made with stucco because it is a durable and cost-effective option for covering and insulating exterior walls. Stucco is a cement-based material that is applied as a thick, paintable mixture to walls. It can last over 50 years depending on the quality and how it was applied, as well as how well it is cared for.
How long does stucco last on a house?
From 1920 to 1980, due to stiff competition, many of the smaller brick companies merged with the larger companies. From Los Angeles came the Pacific Clay Products, Inc., which acquired the Pacific Sewer Pipe Company in Los Angeles and N. During this period also we saw the closing of Remillard, San Jose, Dickey, Simons, and many other large brick plants when the use of building bricks declined in the market place.
/ First brick house in Los Angeles
As paint provides bricks with protective coating, they have been painted with the color which was first used in 1919. A 1983 archeological excavation beneath the wooden floor unearthed artifacts relating to the building’s history. Peter Snell, partner with Long Hoeft Architects and Gus Duffy Architect, were the firms responsible for the Sepulveda Block restoration plans and construction supervision. Señora Eloisa Martinez de Sepulveda built the two-story Sepulveda Block in 1887 in response to the city’s real estate and population boom of the 1800s. As her husband, Joaquin Sepulveda, had died seven years earlier leaving no estate, Señora Sepulveda probably financed the construction of the building on her own.
Eugene Biscailuz Building
Her bedroom reveals much about her Mexican heritage and the popular tastes and styles of the time. It would also reflect some of the places in Los Angeles in the decades following her arrival from Sonora in 1844. The décor of the room shows a practical acceptance of modern technology and contemporary fashion, with its mass-produced walnut furniture and gaslight chandelier. The bedroom has three different wallpapers and a typical flowered carpet. The somewhat-cluttered appearance is characteristic of the period and a sign of modest prosperity. By contrast, the brass bed with its draperies and fancy spread, the Chinese shawl, and the well-tended shrine are representative of Señora Sepulveda’s Mexican upbringing and her strong religious beliefs.
To be clear, they did a little bit of recon ahead of time, which mainly involved visiting the salvage yard a couple of weeks ago just to see if this idea is even feasible. If the only bikes there were basically just frames, and there were no complete or mostly-complete machines on site, the chances of actually succeeding would obviously be a whole lot smaller. As a result, construction is becoming increasingly extensive and expensive in these cities. Skyrocketing rents, lack of supply, and rising housing costs are all contributing factors to the housing shortage, raising the cost of living for all income levels. Rent burdens, overcrowding, homelessness, and racial disparities in housing all persist due to the housing shortage.
Why are homes made with stucco?

Texas came in second with $51.8 billion and Florida followed with $32.7 billion. The amount of new construction has increased significantly in certain states due to the effects of covid-19. Since the early 2000s, there has been rapid buying and selling of properties for investment purposes, leading to an artificially inflated housing market and rising prices. The construction of new homes in these areas can provide employment opportunities and economic boons to these regions. Exurban areas are usually even more remote, offering larger homes and lots on acreages or with more natural landscapes. Suburban and exurban homes are typically designed to accommodate larger families, often with multiple levels and amenities such as pools and outdoor spaces.
In the Fall of 1848, Zins built his two-story brick house on a block of land given to him by Sutter, bounded by M, N, Front, and Second streets, Sacramento. While George Zins laid the bricks, his wife made the mortar and carried the hod. Completed in early 1849, at a cost of $40,000, this was the first brick house in Sacramento. It was later known as the Bininger House, the Green Tea Hotel, the Empire Hotel, and the Pioneer Hotel. Philander Colton and the others of the Mormon Battalion began making bricks in March of 1847 and fired them on May 28, 1847, in Old Town San Diego. At the end of June 1847, the Mormon brickmakers built the first brick building for a courthouse, a replica constructed with modern brick of which stands today on the site at Old Town plaza.
Why can’t California build more housing?
Earthquakes required changes in structural products and building codes that eliminated some companies. Increased use of reinforced concrete also had displaced bricks in the building market. California did not have great paving brick manufacturers like other states mainly because of the scarcity of good vitrified clay deposits. High-quality pavers were shipped from producers outside of California, such as the Denny-Renton Company in Washington. The first paving brick in California was probably that made by the Los Angeles Pressed Brick Company in Santa Monica in 1906.
Adding Windows, Siding, and a Brick Lime-Wash Coating - Fine Homebuilding
Adding Windows, Siding, and a Brick Lime-Wash Coating.
Posted: Wed, 24 Jan 2024 08:00:00 GMT [source]
In 2019, San Francisco and Los Angeles experienced rent increases of over 5%. As a result, these cities have far fewer affordable units available to rent, with just 19% and 21% of units, respectively, deemed to be “affordable” to a family earning the median income. Furthermore, California’s population is comprised of low-income residents, with a large portion of traditionally underserved populations. This means that public funding for housing developments is often allocated to low-cost housing rather than market rate housing. City planners are creating multifamily complexes and mixed-use buildings to create more affordable housing and reduce sprawl.
See homes sold in the Brick area, April 1 to April 7 - NJ.com
See homes sold in the Brick area, April 1 to April 7.
Posted: Wed, 10 Apr 2024 07:00:00 GMT [source]
This company claimed to have the first Hoffman kiln built in the United States. Most of the larger California brick manufacturers used the Hoffman continuous kilns for their rapid and efficient firing of bricks. Some used the round down-draft permanent kilns for finer control of the burn. Most of the mid- to small-sized brickyards used the rectangular up-draft open or field kilns for firing common brick.
Up to 1854, bricks were made and fired right on or near the property of the building project, provided there was enough suitable clay. Many building contractors doubled as brickmakers or hired brickmakers to supply bricks on site. This was true for many of the early brick buildings in the Mother Lode towns along Highway 49, though some bricks were shipped by wagons from Stockton and Sacramento. Just within the city limits, there were 30 brickyards containing 40 brick machines and capable of producing more than 250,000 bricks per day. Harnett, Samuel Carlisle, P.B. Cornwall, F. Burke, Polk and Todd, Pettit and Queen, Fountain Brothers, and Callahan and Ryan.
No comments:
Post a Comment